Transform Utility Capital Project Pipelines with Automation
With design automation, orchestrated data between asset management, GIS, and ERP, and built-in configurable standards, you can save 5-10% on each capital project.
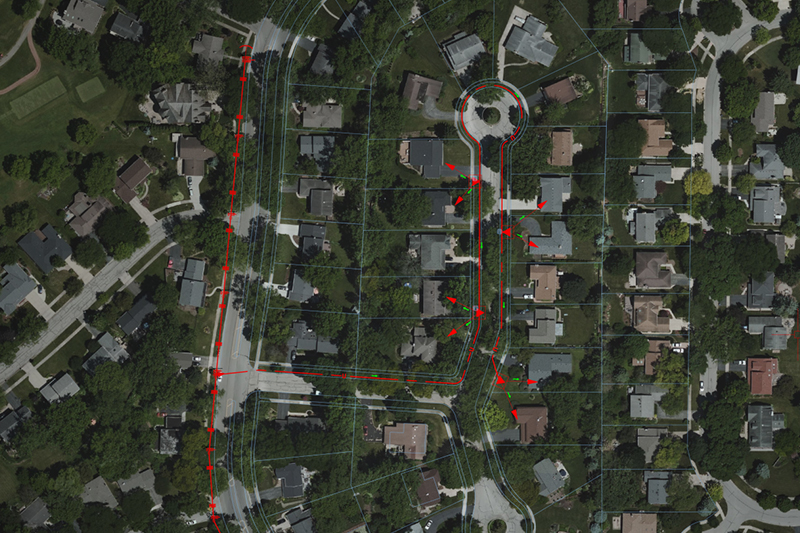
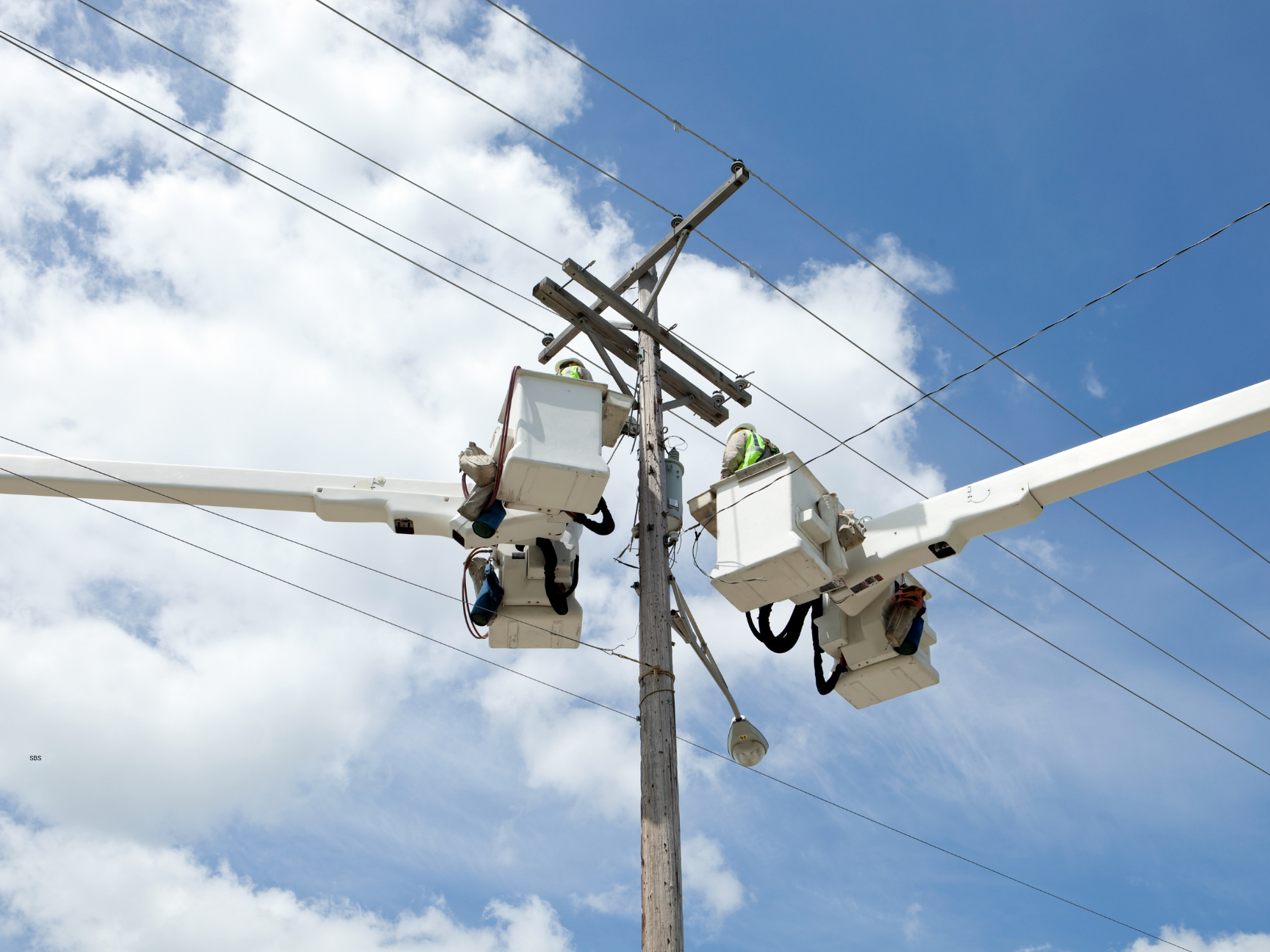
Up to…
- 80% faster design project completion.
- 60% less time spent on change orders and field rework.
- 80% reduction in training time for new designers and engineers.
Comprehensive solutions
SBS design solutions are built for networked infrastructure design.
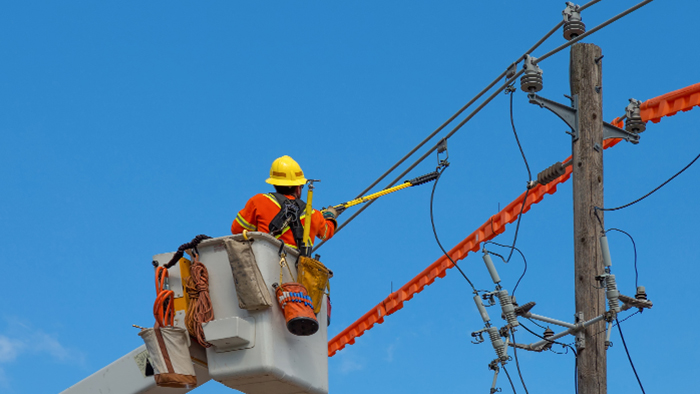
Automated Utility Design (AUD)
Design automation, engineering and design standard templates, and orchestrated asset and location data for energy networks, built on AutoCAD.
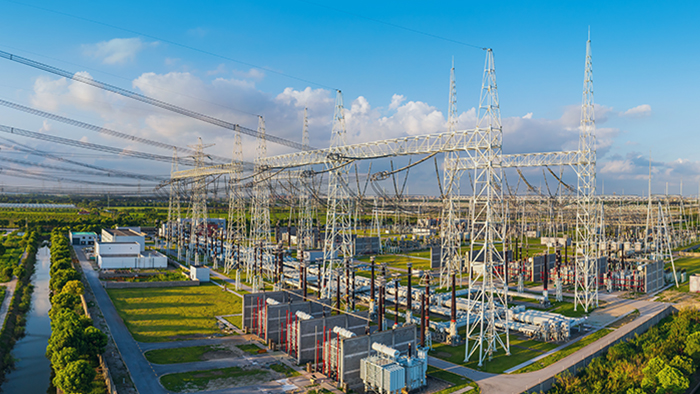
Substation Design Suite (SDS)
Design automation and standards for physical substation designs, available on AutoCAD or Inventor.
Protection & Control design automation and engineering and design standard templates, built on AutoCAD Electrical.
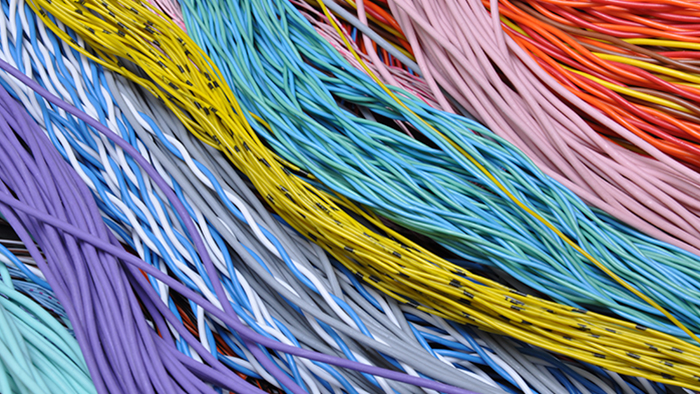
Automated Broadband Designer (ABD)
Design automation, design standard templates, and data orchestration for broadband networks, built on AutoCAD.
Industry-Specific Expertise
Why trust SBS?
- Industry-leading expertise across utility sectors
- Proven leadership team with decades of experience in utility, technology, and AEC businesses
- Scalable technology that grows with your needs
- Trusted by hundreds of utilities and AEC firms across the globe
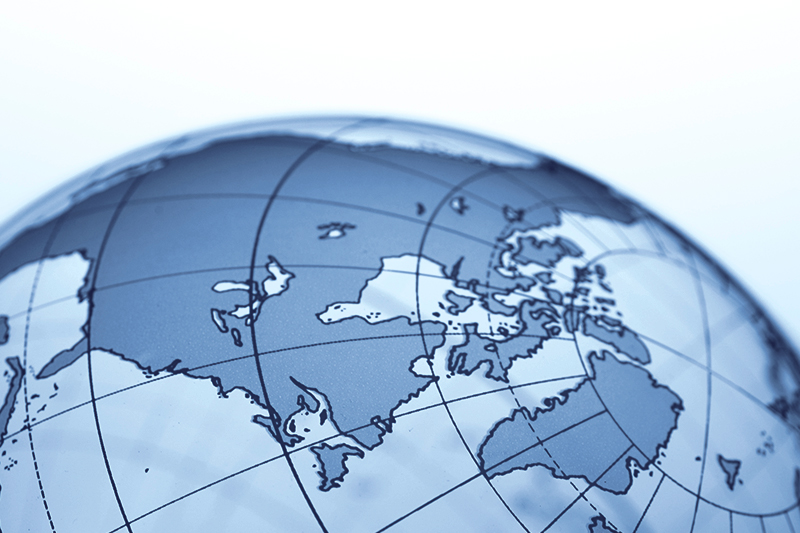
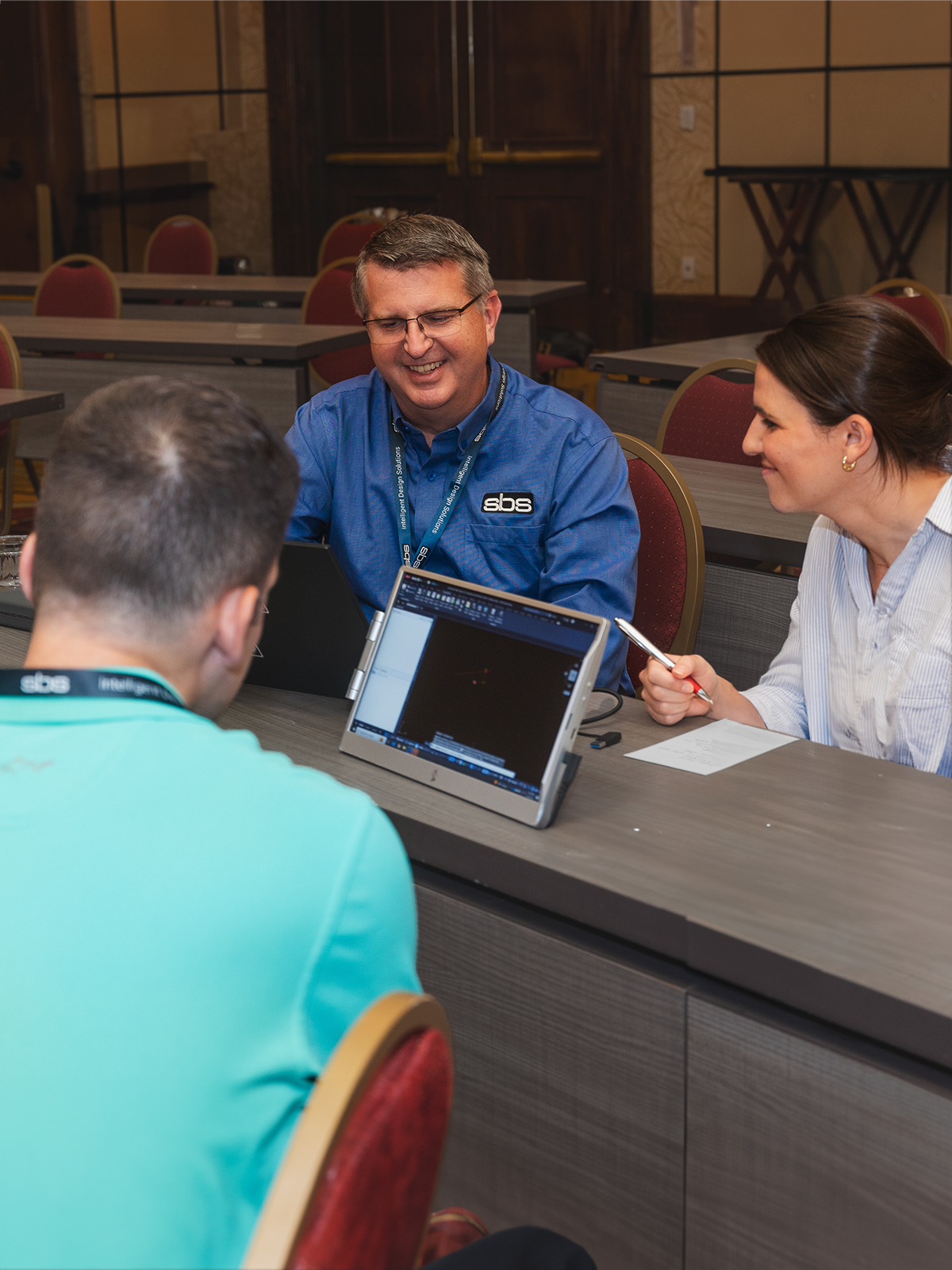
Our customers

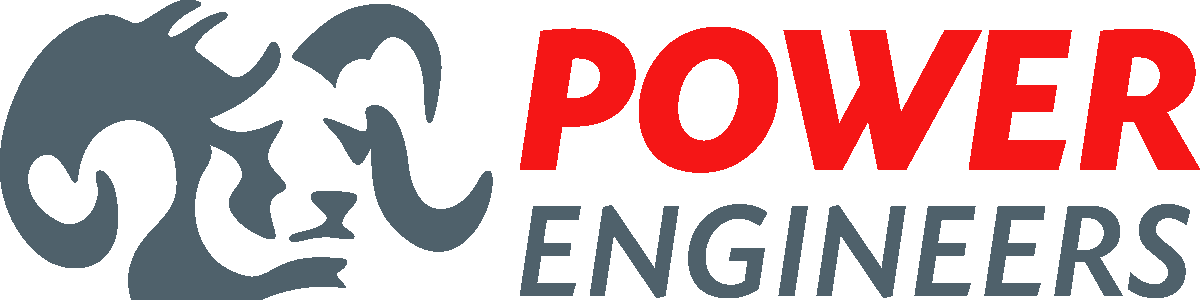

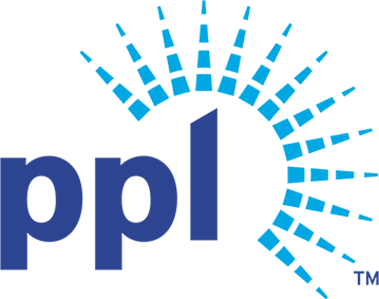
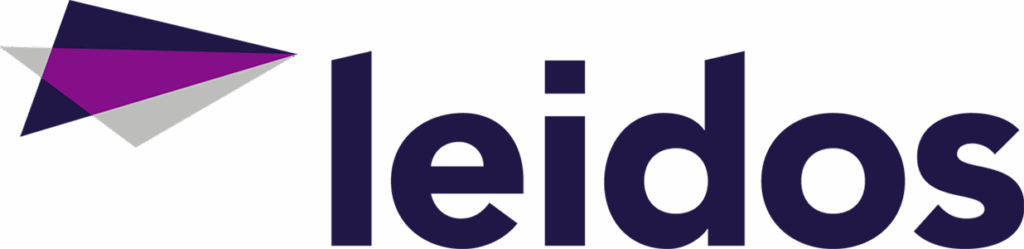
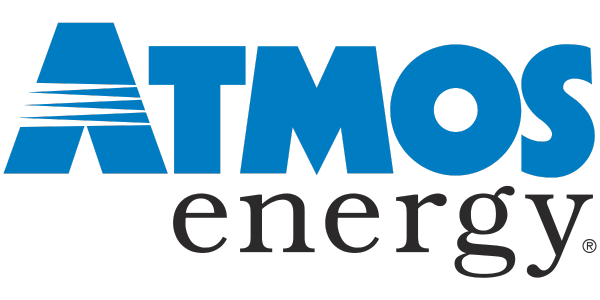