What is it, and why should I care? (Part 1 of 3)
Dennis F. Beck, PE, President/CEO, SBS
Achieving effective design of utility infrastructure has always had its challenges. Distribution system design engineers need to make thousands of modifications to their networks every year. The projects can range from simple network extensions to major capital expansions. Traditionally, these designs have been done in whatever tool is convenient or available, ranging from simple pencil sketches to highly customized tools that are built into other systems, such as a GIS. Actual engineering of designs has historically been limited, but no matter what system is used, the primary challenges are typically related to a lack of integration. Systems involved with utility design can include CAD, GIS, spreadsheets, specialty engineering applications, work order management systems, financial systems, materials management, and scheduling. If you add a mobile component to the front and back end of the process, a large utility can easily have a dozen or more disparate applications involved when creating and executing utility designs.
Fortunately, the latest advances in CAD, GIS, and enterprise integration are enabling a new generation of integrated, intelligent design tools. This post is the first of a three-part series on intelligent design solutions for utilities. This first article explains what is included in an intelligent design solution. The next two articles will highlight business justification and implementation of intelligent design for utility infrastructure.
What Is Intelligent Design for Utilities?
There are three things that make a utility design solution intelligent:
- Ability to be “model-based”
- Support for integrated engineering and standards
- Support for enterprise integration
Model-Based Design
Model-based design refers to the ability to create intelligent, real-world models of the elements that are being designed. The technical basis originates from the software engineering concept of object-orientation and has been extended to CAD and GIS over the past many years. A properly defined model also serves as a digital twin, which is a digital representation of the infrastructure elements. What this means to a utility designer, in a practical sense, is quite important.
In model-based design, elements are no longer just points, lines, and polygons on a drawing. A line, for example, can be a 3D representation of a conductor or a pipe. It has properties to support engineering and materials management. Network topology is modeled to support important business functions such as network trace, which allows the design application to support network analysis or planning for customers that are impacted by loss of service during a construction operation.
Model-based design enables integration. The modeled objects, in addition to their unique properties, have unique identifiers that can be related to the enterprise systems responsible for all aspects of asset life cycle performance. This can range from finance and accounting to engineering, construction, and operations. These properties enable the sharing of these digital twins across all the necessary systems that are involved with creation and fulfillment of the design.
Integrated Engineering and Standards
Once the model is in place, it is possible to combine physical characteristics along with engineering properties and organizational standards to provide a properly engineered design. The role of engineering in distribution network design has been somewhat limited over the years. This has been driven in part by a desire to quickly generate design documents. Unfortunately, this has had negative consequences in the overall effectiveness of network design and related applications that benefit from higher-quality, well-documented designs. The industry acknowledges that there is a new need to raise the standard of engineering in distribution systems. Electric networks are being greatly impacted by smart grid devices, distributed energy resources, and new demand profiles. Gas distribution networks need to properly engineer and document their networks to support regulatory requirements for safety and system integrity management. All these changes require better engineering.
Integrated engineering can occur within the design tool, or in some cases, it might require integration with specialty external programs to perform an appropriate analysis. Internal calculations may include analyzing localized voltage drop or computing pulling tension for underground cable installation. External analysis is often used when performing more advanced functions such as a non-linear structural analysis of poles or the design of a ground grid in a substation. A system with a well-defined model and integrated calculations can readily support most types of analysis. The more common analyses involved in integrated electric distribution engineering include voltage drop, flicker analysis, bending moment, guying design, and underground cable pulling tension.
Enterprise Integration
Utility designs have historically been created in standalone systems. The finished designs are oftentimes printed out and then placed into job folders for work execution. Along the way, the bill of materials is created, data is entered either manually or in a semi-automated manner, and an estimate is performed. Upon completion of the work, the design is redrawn, sometimes several times, into different systems. Not only is this inefficient, but it also takes a lot of time and causes critical systems to become consistently out-of-date. Having an intelligent model of the design eliminates most of these manual steps and replaces them with an automated, timely workflow.
Service-based architectures that work with a data integration hub can provide the necessary integrations to key enterprise systems in a straightforward and configurable manner. Compatible units can be shared from the asset management system; estimates can be derived from an automated bill of material, and the GIS can be kept up to date with the current design information based on preferred workflows. Mobile computing can be integrated at the front end of the design process to support field verification and field construction, and mobile as-built design verification can be performed during the construction cycle. Intelligent design tools facilitate these critical utility workflow integrations with very real opportunities for process improvement.
The example below shows a workflow integration based on SBS Utility DataHub™ and Automated Utility Design™ products:
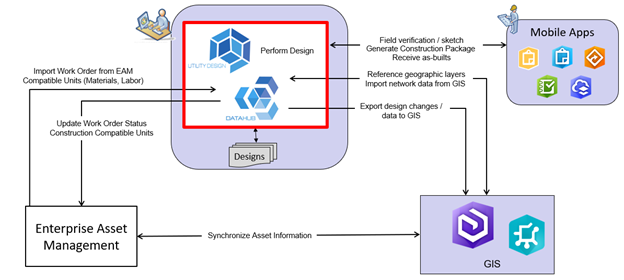
Why Should I Care about Intelligent Design Solutions?
The benefits of intelligent design solutions are starting to become quite clear based on what we have been learning from members of our Peer Utility Group (PUG). In Part 2 – Justifying Your Intelligent Design Solution, we will review customer experiences that have been shared at PUG meetings. The article will also highlight details about mitigated risks and actual benefits:
- Better engineered designs
- Improved safety
- Reduced liability
- Design and construction productivity improvement
- Better information management to support advancements in utility networks